Why Predictive Maintenance Alone Doesn’t Deliver Strategic Advantage
Written by Amanda Derrick
Jul 12, 2023 11:16:30 AM
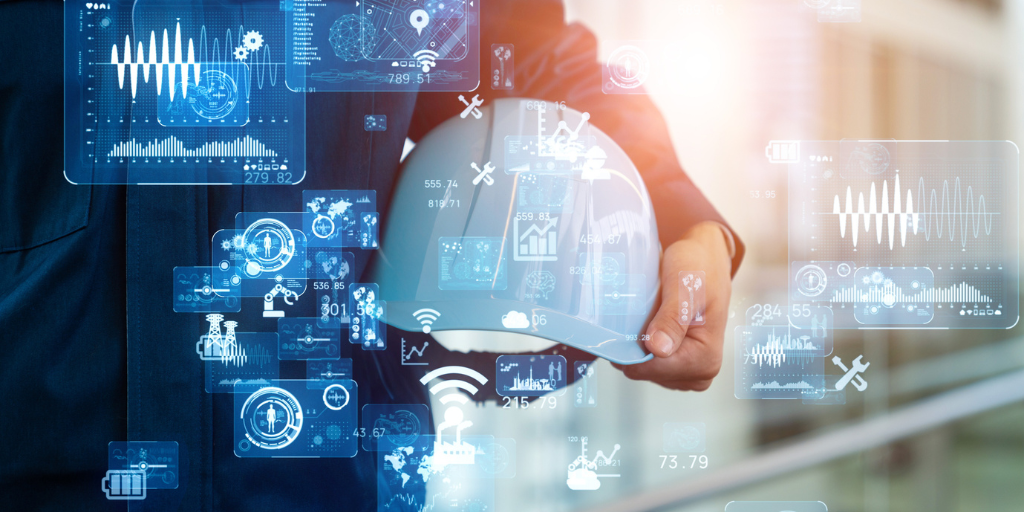
Equipment availability is the difference between success and failure. If a resource is out of service for any reason it means lost revenue. Your data can help keep your equipment running smoothly if you can leverage it correctly, but just predicting failure rates isn’t enough to gain a competitive advantage.
On the surface, keeping things up and running might seem like a simple matter of timely maintenance. If that were true, predicting part failure allows you to fix the part before it breaks. Job done, right? But what good is predicting part failure if you don’t have what you need to fix it? Or the person with the right skills to perform the work isn’t available for two weeks?
Without aligning all the required resources, predictive maintenance is just getting bad news early.
Why does predictive maintenance fall short?
Predictive maintenance seems like a pretty straightforward concept. Look at your data, see what usually fails and when, then work on it before that happens. But there are a lot of reasons why predictive maintenance efforts fail:
- Teams use solutions or datasets they don’t understand. There are many different solutions available to help predict failure rates, but not all of them are created equal. Your maintainers have to have confidence in the insight discovered, which means they need to understand how the solution works, and recommendations must be transparent.
- Stakeholders aren’t invested. Predictive maintenance can feel like a waste of time and resources if leadership doesn’t see the need to stay in front of failure. Teams need to have clear goals and objectives for what they want to achieve through their maintenance efforts so that stakeholders support the program.
- Maintenance efforts are lacking. Proactive maintenance is a continuous process that requires regular monitoring and scheduling. If the program is not consistent, it's unlikely to have a measurable impact.
- No one does deep data analysis at the beginning. The level of data exploration necessary to accurately predict failures requires a skilled team to implement and manage. If you don’t have the right people exploring the right data, you won’t have an accurate read on what to maintain next.
Let’s say your team actually has the data, the solution, and the expertise to accurately predict part failures and overcome these struggles. You know when a part will likely fail. What next?
Predictive maintenance isn’t the whole picture
Predictive maintenance tries to estimate how long a part or component will last. But many industrial systems are inherently dynamic and complex, with numerous interdependencies and variables that can impact overall availability. These complexities make it difficult to develop precise models that accurately predict failures, let alone consider the other factors that impact your actual availability.
Failure predictions also rely on successfully identifying significant patterns within your data. Unfortunately, not all failure modes exhibit indicators that can be easily detected. Some failures may occur sporadically or randomly without any discernible patterns, making it challenging to predict when they will happen. Furthermore, the occurrence of rare or unique failure events may not be adequately captured in historical data, reducing the accuracy of predictive models.
Even if you can predict failures, there’s much more data that needs to be considered if you’re going to handle failures well. And how you handle failures is what makes the real difference in your availability rate and overall success.
Introducing Integrated Resource Optimization
Proactively managing resources to optimize their availability means managing inventory, scheduling maintenance professionals, and identifying the right time to go offline that minimizes disruption. The reward is increased uptime, lowered risk, fewer costly repairs, happier customers, and more revenue potential.
Virtualitics has developed a comprehensive solution designed to keep your resources, and your operations, running smoothly that puts all the pieces of the puzzle together so you can optimize your resources–we call this practice Integrated Resource Optimization (IRO).
Virtualitics IRO is a suite of workflows that deliver mission-critical insight across four key areas:
- Predictive Maintenance (PMX): Calculate the remaining useful life and evaluate risk at subsystem and component levels.
- Inventory Optimization (IO): Identify current and future supply chain limitations and bottlenecks and ensure resources are available.
- Resource Assessment (RC2A): Data from PMX and IO provides production decision-makers with full operational resource insight.
- Mx Schedule Optimization (MSO): Combined PMX, IO, and RC2A results to optimize scheduled maintenance plans.
Our proprietary solution enables the assimilation of parts, equipment, and human resources so that leadership is aware of resource constraints and can provide strategic decisions not just for maintenance, but for inventory, people management, and facilities. That means that teams don’t just understand failures; they know they have the ability to proactively address issues and keep their equipment and business running smoothly.
Stay tuned to the Virtualitics website to learn more about Integrated Resource Optimization.