Optimizing maintenance, logistics, and supply management with Virtualitics
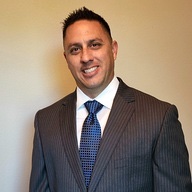
Written by Jerami Reyna
Nov 9, 2022 1:37:53 PM
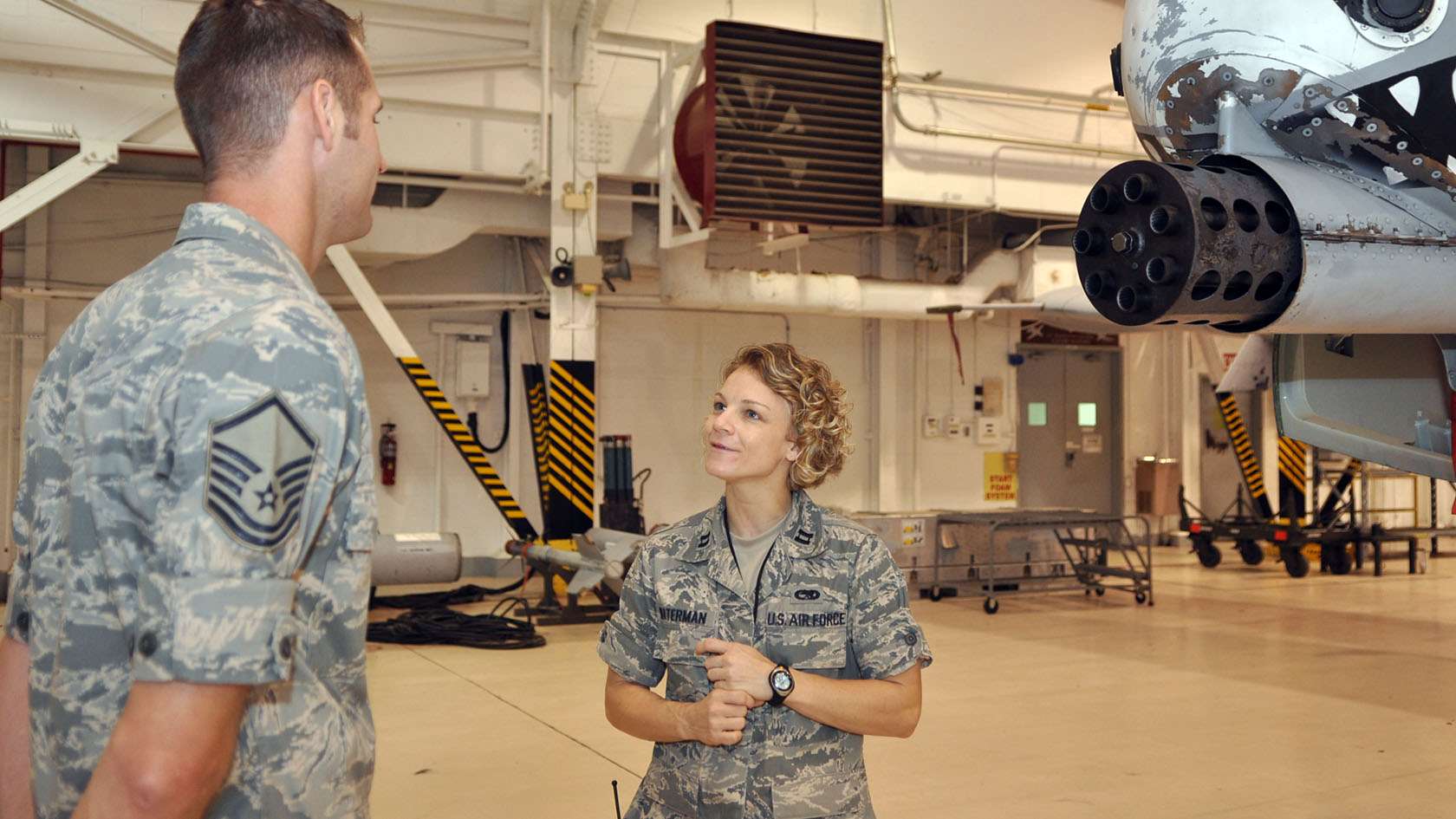
Multitasking? Great! You can listen to this blog post by clicking above or find our podcast, Intelligent Data Exploration, on major podcast platforms.
Sometimes when you’re managing things—parts, people, processes, and logistics—it can feel like you’re always reacting to something. While the world aspires to predict everything from the weather to when we need to change the oil in our vehicles, we can’t always know when a part will fail, someone will call in sick, or a supply chain will hit a snag.
We try to anticipate what we can, based on experience. Then we’re forced to react to everything else because predicting lead time, appropriate inventory, and time to repair is incredibly complex with many variables in play. Somewhere, in all that data that you’re capturing about your operations, the information you need is hidden. But the challenge lies in connecting those dots and pulling out the insight you need to build an AI model and put predictive maintenance workflows in place.
Analyzing maintenance and supply data with Virtualitics
Maintenance operations create and collect a lot of information—parts inventory lists, staffing plans, procedures, repair times, repair logs, shift planning, and so much more. But often these items are only part of record keeping, not used as a resource for data exploration to predict failures and improve outcomes because finding the insight in a dataset as vast and varied as this is a challenge.
Traditional BI tools would require an incredible number of two-dimensional graphs to illustrate the data, and those graphs wouldn’t be able to express the connections between so many variables. And the data in the rich text documents is often left completely untapped.
But by applying out-of-the-box AI (Intelligent Exploration) to evaluate historical maintenance data across data sets and data types, Virtualitics enabled data scientists to quickly determine certain components’ Mean Time to Failure (MTTF) and what factors contribute to that failure. Because Virtualitics’ Intelligent Exploration can analyze an unlimited number of attributes at once, you can throw in every possible contributing factor and it can quickly zero in on the drivers of product failure.
While predictive information like MTTF is insightful, that data alone is just part of the answer. The connections between key drivers like failure data and your maintenance and logistics activities like time to repair and inventory optimization are the places where you’re able to implement strategic practices that will positively impact your readiness rate.
Intelligent Exploration allows teams to understand supply chain constraints in the context of failure rates and availability in order to better support maintenance actions. With network graphs and AI-guided insights, supply managers, schedulers, and maintenance managers can work together with the data science teams to understand how to proactively balance inventory availability with budget and manpower.
Working as a team with a clear understanding of the drivers in all of their data, they can evaluate demand signals to determine the best ways to optimize all their resources. Virtualitics algorithms can also identify outliers in data, allowing teams to consider edge cases and how they might accommodate sudden needs.
With all of this insight, the data science team can build an AI model that can predict when certain components will fail with a high degree of confidence in time for the logistics teams to plan accordingly. Virtualitics Intelligent Exploration helps to unearth the critical data that should inform an accurate predictive model that allows maintenance leadership to determine how to become less reactive and more proactive.
Explainable AI to guide process optimization
Creating a usable, valuable predictive model for preventative maintenance is a challenge that Virtualitics solves, but the other piece of the puzzle is ensuring that the end users understand and trust it enough to use it. Because the users aren’t analysts– they’re people like me whose main job was to maintain equipment and keep things moving.
I was the lead maintenance manager for an aircraft maintenance unit, responsible for balancing aircraft maintenance and flying requirements for my respective unit. Shortly after I started the position, an increase in COVID cases drove a change in protocol in order to keep our personnel safe which drastically reduced how many personnel I had available to commit to fixing airplanes. During COVID my maintenance capability varied from week to week and many times from day to day. Managing it all was a constant effort.
A platform like Virtualitics could have given me a deeper understanding of my resources and availability, so I could better assess our maintenance capability. Predictive workflows delivered via the Virtualitics AI Platform provides recommendations for actions teams can take to improve processes, backed by clear explanations of the reasons behind them. That would’ve been a huge help to me, and I’m very happy that we can provide that resource to our customers.
Collaborating for Data-driven Optimizations
If your team is ready to move toward model-based optimization, it’s Intelligent Exploration that ensures that your model will be based on the right drivers and actions and provide value to your organization. And with explainable AI powering the dashboards and workflows, you can trust that your intended audience is able to quickly identify their current status, see potential roadblocks, and plan for the optimal use of their resources.
Transition from reacting to unscheduled maintenance events to proactively scheduling assets and manpower for repair. Virtualitics’ takes a holistic view of the maintenance effort in order to make data actionable.