What Is Industry 4.0? State of Analytics in Industry 4.0
.png)
Written by Virtualitics
Sep 30, 2021 6:57:00 AM
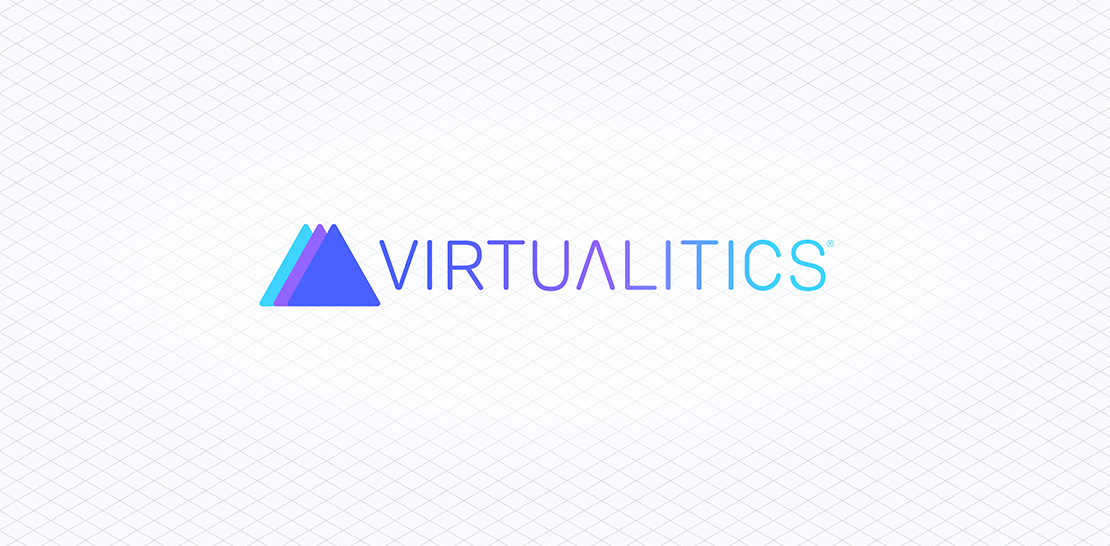
The fourth industrial revolution (Industry 4.0) is well underway, as traditional manufacturing and industrial practices are increasingly augmented with “smart” technology to automate processes, monitor performance, and diagnose issues.
The sensors within these connected systems generate vast amounts of data across a countless number of variables. With the right analysis tools, this data can be used to drive efficiencies, reduce downtime, minimize unscheduled maintenance, and save the business time and money.
Industry 4.0 Data Analytics Challenges
The process of integrating high-tech monitoring and analytics into these complex industrial and manufacturing environments is not without its challenges.
Although some of the data analytics obstacles found in Industry 4.0 are a natural part of integrating new technology into established systems and processes, others are more fundamental in nature.
Siloed Operational Knowledge
In a manufacturing setting, knowledge is often siloed by department, with little visibility between groups. When there is a performance problem, equipment operators, manufacturers, field technicians, and maintenance workers all may have a piece of the information needed to solve the problem. But with no way to explore the relationships between the pieces, getting to the root cause of an issue is a slow and inefficient process.
Difficulty of Extracting Meaningful Insight from Large Amounts of Data
The data gathered in industrial and manufacturing settings comes from many different sources, which makes it extremely difficult to find connections between how data derived from one component impacts the data from a seemingly unrelated operation. To further exacerbate the problem, data may also be structured or unstructured, making identifying interrelationships even more complicated.
Skilled Worker Shortage
The lack of skilled technology and data science workers isn’t an Industry 4.0-specific challenge, but with more types of enterprises now relying on technology and data to run their businesses than ever before, the issue is reaching critical mass. In fact, a recent Gartner survey found that IT executives rate lack of technology talent as the most significant adoption barrier to 64 percent of emerging technologies. That’s a huge increase from the 4 percent reported in 2020.
How AI and Multi-Dimensional Data Visualization Help Solve Industry 4.0 Data Analytics Challenges
In today’s data-fueled industrial and manufacturing environments, connecting the dots between disparate data sources and using that information to drive action is critical. As Industry 4.0 continues to mature, data analytics must evolve to ensure enterprises realize the full potential of their embedded technology investments.
Flat, two-dimensional data representations can’t provide the level of insight needed to close information gaps and drive decision making. Artificial intelligence and multi-dimensional visualization tools are essential elements in this new industrial revolution. Together, these technologies provide deep visibility into interrelationships that isn’t possible with traditional analytics and visualizations.
Multi-Dimensional Visualization
Multi-dimensional visualizations enable analysts and stakeholders to find the “whys'' behind the data. Knowing why equipment is behaving a certain way or why a sensor alert is frequently triggered helps teams maximize system performance, find the root cause of chronic issues, and take a proactive approach to preventing system failures and downtime.
In manufacturing and industrial services, data-driven decision-making is the most impactful; however, many mission-critical decisions are made by non-technical stakeholders. Data visualization takes complex, multi-sourced information and translates it into a visual model that is easily understood by data scientists and the C-suite alike.
For example, applying AI routines in conjunction with data visualizations enables analysts to identify which variables in a dataset have the greatest impact on the target variable. Using this information, the data analytics application can recommend the most appropriate visualization to interpret and explain why the findings are significant and provide easy-to-understand insight or validation around an issue.
Predictive Analytics
One of the most valuable outcomes of Industry 4.0 is the ability to predict and proactively address system and component failures that lead to lost productivity and revenue.
Predictive modeling leverages machine learning and AI-driven pattern recognition processes to quickly identify anomalies and trends within the data.
For example, predictive models can take both structured and unstructured data from disparate sources and determine which parts or systems are most likely to fail within a given period of time. This information is then integrated into maintenance workflows and systems, which ensures the at-risk components are inspected and replaced before a failure causes any downtime.
What’s Next for Industry 4.0 Data Analytics?
Looking ahead to the widespread rollout of technologies like 5G and the growing adoption of IoT in manufacturing and other industrial applications, it’s impossible to predict where Industry 4.0 will end and the next technology era will begin. However, we can be sure that data will play an even larger role in business and industry in both the short and long term.
As the volume of data continues to grow, analytics capabilities will have to keep pace to ensure the data can be used to provide value and insights to drive decision-making and process and performance improvements.