DATA VISUALIZATION, IOT, DATA ANALYSIS
How Industry 4.0 Can Utilize Machine Learning
.png)
Written by Virtualitics
Dec 21, 2021 5:53:00 AM
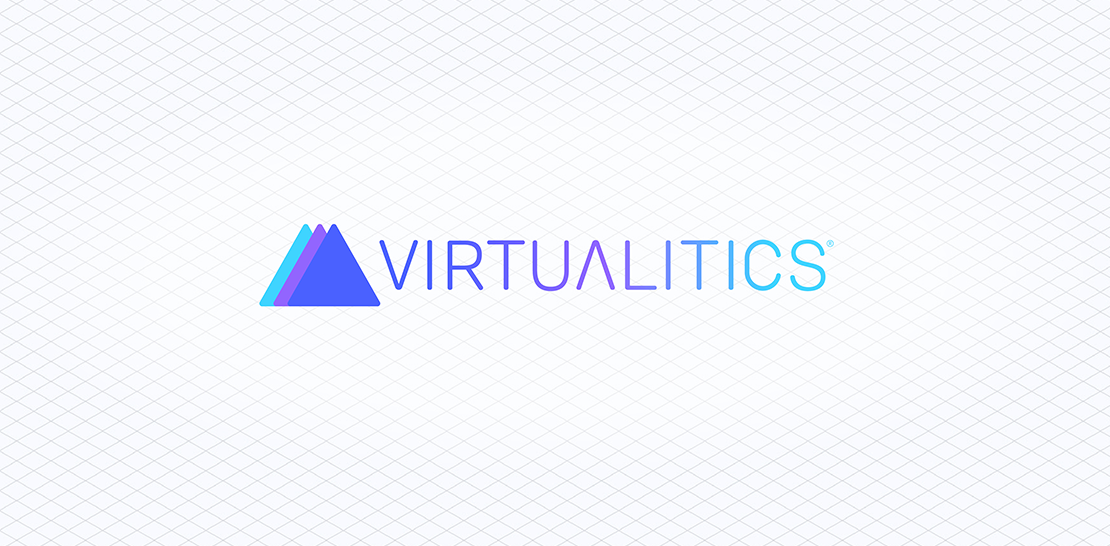
In 2011, the German government coined the term “Industry 4.0” to describe the growing application of automation and data connectivity to manufacturing and industrial processes. Today, the Fourth Industrial Revolution is in full swing, and machine learning is playing a pivotal role in advancing the movement.
Talk of artificial intelligence in manufacturing and industrial settings has always sparked fears that human workers will become obsolete. However, in practice, machine learning creates an opportunity for humans and technology to work in concert to achieve greater efficiency, resilience, and consistency.
The Demands of Industry 4.0 to Leverage Machine Learning
The power of applying machine learning to industry lies in the ability to leverage data in ways the human brain cannot accomplish alone. For the industrial sector to take advantage of machine learning, it requires historical and live data collection from various streams, aggregation of data from disparate sources, and integrated platforms for data analysis and 3D visualizations.
For example, a general Industry 4.0 use case may entail the following steps:
-
Data is collected from sensors located at critical points in the manufacturing process.
-
The data is transferred to the cloud, where it is analyzed using machine learning algorithms.
-
The system generates multidimensional visualizations that provide a 360-degree view of the data, including process efficiencies and performance roadblocks.
-
Operators use this information to trigger maintenance or optimize functions within the process.
At a broader scale, machine learning helps manufacturing and industrial organizations do everything, from better understanding their users’ needs to proactively initiating equipment repairs that prevent breakdowns in mission-critical systems.
The Impact of Machine Learning on Manufacturing
Machine learning enables systems and algorithms to improve by “learning” from experiences. This continuous adaptation in response to new and updated information allows manufacturing organizations to optimize their operational efficiency and their processes.
In recent years, machine learning technology has paved the way for smart factories. These highly connected facilities use Internet of Things (IoT) devices, sensors, software, and analytics to digitize the manufacturing process, continually monitoring production performance and capturing data. With this high volume of extremely targeted data available for analysis, machine learning enables stakeholders to make more informed decisions that result in more successful business outcomes.
6 Ways Machine Learning Makes Industry 4.0 Smarter
1. Real-Time Quality Control
Machine learning reduces incidents of manufacturing defects and quality issues by integrating with video streaming devices and smart sensors to assess product quality in real time throughout the manufacturing process.
Operators receive alerts about potential issues during production so they can correct them early. This level of inspection and error detection wouldn’t be feasible if it had to be done manually, so machine learning helps improve product quality and, by extension, customer satisfaction.
2. Reduced Downtime with Predictive Maintenance
Machine learning enables predictive analytics, which, in turn, makes predictive maintenance possible. Sensor-equipped components feed performance information to the machine learning system. Using AI routines and algorithms, machine learning tools detect the need for maintenance before a breakdown occurs, which minimizes downtime and reduces the expense of unplanned repairs.
3. Improved Performance
Pinpointing the root cause of performance issues can be tricky. Machine learning algorithms take data from equipment sensors and other unstructured data sources and create visualizations that make it easier to isolate the cause of problems within the system.
By identifying patterns and relationships that are often hidden within the data, machine learning tools make it possible to see how different system components and environmental factors impact performance so operators can quickly correct issues at the source.
4. Autonomous Machinery
Warehouse and factory work is notoriously dangerous for humans. Machine learning enables robotic operators to take over repetitive or high-risk tasks, which makes manufacturing and fulfillment processes safer and more efficient.
5. Demand Prediction
Miscalculating demand can lead to wasted time, effort, and product at one end and product shortages and customer dissatisfaction at the other. Machine learning allows operators to track and monitor historical data for demand and other influencing factors. This insight makes forecasting more accurate so production can be adjusted appropriately to reduce waste and maximize revenue opportunities.
6. Inventory and Supply Chain Management
Industry 4.0 relies on automated inventory and supply chain management tools to drive efficiencies and mitigate risk. Machine learning and IoT services provide real-time insights and visibility into inventory and supply chains so operators can identify bottlenecks early while proactively maintaining appropriate inventory levels.
Achieve Greater Efficiency, Productivity, and Reliability with Machine Learning
In today’s highly connected business environments, data is king. For the manufacturing and industrial sectors, machine learning makes it possible to harness the power of data to increase efficiency, increase critical system availability, and reduce costs.
With the rise of Industry 4.0, AI-driven visualizations are democratizing data analytics by making data accessible and understandable for all stakeholders, not just the data scientists.